Se você busca melhorar a eficiência operacional da sua empresa, precisa saber utilizar indicadores de manutenção. Eles são métricas que permitem criar uma operação de produção eficiente, inovadora e centrada na qualidade.
Mas, por que é importante trabalhar com indicadores de manutenção? É simples.
A manutenção industrial tem como objetivo manter a fluidez de processos e reduzir ao máximo gastos e problemas relacionados a paradas operacionais, estando diretamente relacionada à qualidade e eficiência. Nesse sentido, utilizando os indicadores de manutenção corretos, é possível economizar dinheiro, reduzir riscos e aumentar ao máximo a performance da indústria.
Quer entender um pouco mais sobre indicadores de manutenção? Continue a leitura para conhecer os principais KPIs desse grupo e como utilizá-los.
O que são indicadores de manutenção?
Indicadores são também chamados de KPIs (Key Performance Indicators ou indicadores-chave de desempenho). Os indicadores de manutenção referem-se às métricas fundamentais para mensuração do desempenho da cadeia de produção de uma indústria.
Em suma, os indicadores de manutenção são essenciais para medir a qualidade dos produtos, identificar incoerências entre o desempenho alcançado e o desejado, melhorando a satisfação do cliente.
Além disso, o monitoramento desses KPIs permite efetuar a manutenção preventiva, controlar a disponibilidade de equipamentos e potencializar a performance das máquinas e processos.
Com isso, é possível reduzir prejuízos e custos, melhorar a tomada de decisões, e ainda prever, amenizar e corrigir falhas. Ou seja, o uso dos indicadores de manutenção pode contribuir muito para alcançar os objetivos da empresa.
Existem três tipos de indicadores de manutenção (estratégicos, táticos e operacionais), que serão abordados a seguir.
Indicadores de manutenção estratégicos
O nível estratégico é responsável por visualizar o negócio de maneira ampla e tomar decisões com base em dados e tendências de mercado. Neste caso, os KPIs estão mais atrelados à missão de determinado setor e aos objetivos de negócio.
Geralmente, são utilizados para ajudar no planejamento estratégico da manutenção. Além disso, permitem à empresa inovar e aumentar a produtividade, a lucratividade e a competitividade do negócio.
Os indicadores de manutenção estratégicos estão relacionados, por exemplo, a decisões sobre aquisição e/ou substituição de máquinas.
Indicadores de manutenção táticos
Já no nível tático, a gestão deve se planejar e se organizar para alcançar os objetivos e garantir o desempenho dos processos. Assim, os KPIs são usados para medir o alcance das metas e servem para garantir que as estratégias definidas realmente serão atingidas.
Indicadores de manutenção táticos envolvem auditorias, logística e segurança do trabalho, por exemplo. Eles estão relacionados às necessidades para atender volumes e prazos de produção, com o objetivo de manter padrões de qualidade, organizar fluxos de trabalho e aumentar a produtividade sem elevar custos.
Indicadores de manutenção operacionais
Indicadores de manutenção desse tipo estão focados na execução e acompanhamento de processos visando a excelência operacional. Portanto, estão ligados a aspectos de manutenção da operação.
Os KPIs de manutenção operacionais estão voltados a recursos (tanto de pessoas quanto de peças) para manutenção dos ativos. Eles são importantes para manter o ciclo produtivo em funcionamento conforme o planejamento e as expectativas, porque garantem o bom desempenho de máquinas e equipamentos, além de evitar paradas na produção.
Quais são os principais indicadores de manutenção?
Agora que você já sabe a importância e os benefícios dos indicadores de manutenção na gestão industrial, é hora de aprender a utilizá-los. A seguir, listamos os principais KPIs para usar na sua empresa.
MTBF (Mean Time Between Failures) – Tempo médio entre falhas
O “tempo médio entre falhas” é um indicador de manutenção usado para medir a confiabilidade dos ativos. Ou seja, serve para mensurar o quão confiável sua máquina ou equipamento é.
Conhecido pela sigla MTBF (em inglês, Mean Time Between Failures), esse KPI é calculado dividindo o tempo operacional total pelo número de falhas:
MTBF = Quantidade de minutos em que o equipamento trabalhou em bom funcionamento / Número total de falhas
O MTBF é essencial para programar a manutenção preventiva, direcionar ações adequadas para cada máquina ou equipamento, evitar paradas na produção e aumentar a produtividade dos ativos.
Vamos ver um exemplo para ficar mais claro. Imagine uma máquina que trabalha 10 horas por dia em perfeito funcionamento. Essa máquina apresenta falhas duas vezes ao dia, e sua manutenção leva 15 minutos para acontecer.
O cálculo, neste caso, seria:
MTBF = (10 x 60) – 30 / 2 = 285 minutos
Sabendo o tempo médio entre as falhas, é possível planejar a manutenção preventiva a fim de reduzir essas ocorrências. Quanto maior o MTBF, melhor. E a recomendação é que esse KPI seja calculado individualmente para cada equipamento.
MTTR (Mean Time To Repair) – Tempo médio de reparação
O MTTR significa o tempo médio de reparo (em inglês, Mean Time to Repair). É um KPI referente à mantenabilidade. Ou seja, a capacidade de uma máquina ser recolocada em condições de executar suas funções esperadas, dentro das condições de uso especificadas.
Tem a seguinte fórmula:
MTTR = Quantidade de minutos em que o equipamento ficou parado para reparo / Número total de reparos
No caso do exemplo acima, em que a máquina parou duas vezes durante o dia e sua manutenção levou 15 minutos, o cálculo seria:
MTBF = 30 / 2 = 15 minutos
Isso significa que a produção deve se programar para absorver, em média, 15 minutos de reparo para o maquinário.
O MTTR é o tempo entre a falha e o momento em que o sistema volta a operar perfeitamente. Sendo assim, ele indica a eficiência da equipe de manutenção para efetuar o reparo. Quanto menor o MTTR, melhor.
Disponibilidade – Availability
O indicador de disponibilidade (também usado em inglês – Availability) refere-se ao tempo médio em que um equipamento se encontra disponível para operar. Esse KPI ajuda a descobrir o tempo que a máquina ficou à disposição da empresa.
A fórmula para calcular a disponibilidade é:
A = MTBF / (MTBF + MTTR) x 100
Quanto maior a disponibilidade, melhor, já que isso significa que o equipamento está cada vez mais disponível para ser usado.
Confiabilidade – Reliability
Já a confiabilidade (R – Reliability) significa a capacidade de um equipamento cumprir as suas funções esperadas durante um determinado período.
É bem comum a confusão entre disponibilidade e confiabilidade, mas elas são métricas diferentes. A confiabilidade avalia a performance do ativo em um espaço de tempo específico, enquanto a disponibilidade mede o desempenho desse ativo durante toda sua vida útil.
Além de segurança e qualidade, a confiabilidade ajuda a medir probabilidades de falhas e a evitar erros. Sua fórmula é:
R (t) = e^⁻λ.t
A letra “t” refere-se ao tempo que se quer medir e deve seguir a mesma unidade do MTBF (horas, minutos, etc); a letra”e” significa a base dos logaritmos Neperianos e vale 2,71; e λ é a taxa de falhas, calculada pela seguinte fórmula:
λ = 1 / MTBF
Backlog
Backlog nada mais é que o tempo que seria utilizado para executar a meta de serviços com a força de trabalho disponível naquele período. Consequentemente, é o indicador de manutenção que se altera diariamente, uma vez que os trabalhos são finalizados e novas demandas aparecem constantemente.
O backlog, portanto, é um indicador que o gestor deve almejar a estabilidade. Isto é, quanto mais estável, melhor.
Seu cálculo utiliza como base o HH OS, que soma os valores de “homem-hora” (HH, uma medição sobre o nível de produtividade do trabalho por hora) em relação à OS (ordem de serviço). A OS pode ser classificada como: pendente, planejada, programada e executada.
Nesse sentido, o HH resulta do valor de HH total (HHT), multiplicado pelo percentual de produtividade do colaborador:
HH disponível = HHT x percentual de produtividade (%)
Após esse cálculo, já é possível calcular o backlog, cuja fórmula é:
Σ HH OS Planejada + Σ HH OS Pendente + Σ HH OS Programada + Σ HH OS Executada / HH disponível.
O backlog tem como objetivo compreender o volume de trabalho da equipe. Ou seja, se está excessivo ou não, por exemplo.
CPMV (Custo de Manutenção sobre Valor de Reposição)
Outro indicador de manutenção muito relevante é o CPMV, ou Custo de Manutenção sobre Valor de Reposição. Esse KPI se destaca como uma ferramenta analítica para apurar o custo de manutenção atribuído a cada equipamento, permitindo avaliar se é mais vantajoso manter o ativo atual ou investir na aquisição de um novo.
O CPMV é recomendado especialmente em equipamentos de elevada criticidade. Sua fórmula de cálculo é bastante simples, conforme descrito abaixo:
CPMV = (Custo Total de Manutenção / Valor de Compra de um Novo Ativo) x 100
O resultado será a taxa de CPMV, que deve estar em até 6%. Se o resultado extrapolar esse limite dentro de um ano, é necessário fazer a troca do equipamento.
Isso significa que, quando se fala em CPMV, quanto menor o valor encontrado, melhor, uma vez que a máquina não precisa ser substituída e ainda é vantajoso mantê-la por mais algum tempo, apesar de suas manutenções.
CMUP (Custo de Manutenção sobre Unidade Produzida)
O CMUP é um indicador essencial para manter a competitividade dos preços. Seu propósito é avaliar o impacto dos custos de manutenção na formação do preço do produto comercializado.
Esse KPI evita previne repasses excessivos nos valores finais, evitando encarecer o produto e, consequentemente, afastar os consumidores. No cálculo, é preciso levar em conta não apenas os custos de manutenção diretos, como materiais e mão de obra, mas também os custos indiretos, como energia elétrica e transporte.
CMPU = Custo de Manutenção / Total de Unidades Produzidas
Em média, o custo de manutenção é de 4% em relação ao faturamento do negócio. Portanto, ao calcular a CMUP, certifique-se de que esse indicador não ultrapassa demais os valores praticados pelo mercado.
CMF (Custo de Manutenção sobre Faturamento)
O CMF, que significa Custo de Manutenção sobre Faturamento, é um indicador que avalia os efeitos da manutenção na empresa. Ele serve para verificar se o setor está gerenciando bem os recursos e se a equipe está gastando muito com reparos e consertos.
No CMF, estão envolvidas despesas com materiais, terceirização de serviços, mão de obra interna, depreciação dos maquinários e perda de faturamento. Trata-se de um indicador que precisa estar sempre positivo, uma vez que tem impacto direto sobre a estabilidade financeira do negócio.
A sua fórmula é:
CMF = (Custo Total de Manutenção / Faturamento Bruto) x 100
Após esse cálculo, no entanto, ainda há trabalho a ser feito. Isso porque é preciso utilizar o resultado como um comparativo de mercado, observando se a taxa encontrada é um indicador saudável para a empresa.
Distribuição por tipo de manutenção
Esse indicador mostra a distribuição percentual de cada tipo de manutenção realizada na empresa.
Geralmente, é aconselhável que o gestor de manutenção limite o percentual de práticas corretivas não planejadas, buscando sempre minimizá-las.
O índice de distribuição por tipo de manutenção também serve como base para calcular outros indicadores, como as horas-homem empregadas em cada tipo de reparo.
MPd e MP (Cumprimento dos Planos de Manutenção Preditiva e Preventiva)
Os indicadores de cumprimento dos planos de manutenção preditiva (MPd) e preventiva (MP) mostram o quanto o planejamento de manutenção foi, de fato, executado.
Mas, primeiro, é importante entender a diferença entre esses dois tipos de manutenção. A preditiva é aquela baseada nas condições das máquinas e é muito importante para prever a falha ou a quebra do ativo, reduzindo a necessidade de manutenções corretivas e preventivas.
Alguns exemplos: monitoramento de vibrações e ruídos, medição de temperatura, análise de correntes e descargas elétricas.
Já a manutenção preventiva é programada, realizada periodicamente, como, por exemplo, ascomo por exemplo as inspeções, lubrificações periódicas e calibração de ativos. Esse tipo de manutenção visa diminuir ou impedir falhas no equipamento.
O cálculo do MPd e MP é basicamente o mesmo, mudando apenas o tipo de manutenção: tarefas realizadas do plano de manutenção divididas pelas ações programadas do plano de manutenção. Depois, é só multiplicar por 100 para chegar à porcentagem, como você pode ver a seguir:
MP ou MPd = Tarefas realizadas no programa de manutenção preditiva ou preventiva / Tarefas programadas no programa de manutenção preditiva ou preventiva
Como analisar corretamente os indicadores?
Agora que você já sabe quais são os principais indicadores de manutenção, é preciso conhecer as melhores práticas para gerenciá-los. Isso porque, apesar de extraí-los de forma correta, deve-se ter em mente quais são as suas aplicabilidades. Nesse sentido, os próximos passos a serem adotados são:
Passo 1 – Alinhe o trabalho
Ter objetivos claros e alinhados de ponta a ponta com sua equipe é imprescindível para que os indicadores façam sentido na organização. Como falamos, de nada adianta extrair um número sobre apenas um processo ou um único fluxo de trabalho. É preciso olhar para toda a operação de forma integrada.
Nesse sentido, deve-se trabalhar para minimizar ruídos de comunicação, além de percorrer metas bem estruturadas e traçadas para todo o time.
Passo 2 – Categorize as informações
Para fazer a análise dos números extraídos, o gestor pode partir de dois pontos de vista: o quantitativo e o qualitativo. De forma complementar, essas visões auxiliam na compreensão dos mesmos resultados sob mais de um aspecto, o que gera ainda mais insights de gestão e alinhamentos estratégicos.
A análise quantitativa é o resultado numérico. Assim, ela tem como característica a objetividade. Já a análise qualitativa depende de um estudo sobre o número revelado. Por isso, um time de especialistas bem treinados é capaz de compreender diversos aspectos que explicam o número extraído, com base em técnicas de mercado.
Passo 3 – Crie gráficos
É importante acompanhar estes indicadores constantemente e fazer comparativos entre dias, meses e anos. Dessa maneira, uma forma de analisar visualmente melhor esse resultado é com a criação de mapas, diagramas e gráficos de desempenho. Isso facilita na hora de mapear oportunidades e problemas ao longo da gestão.
Além disso, ajuda na apresentação de relatórios de gestão, que ficam mais fáceis de serem compreendidos por todos os demais gestores e executivos.
Checklist de manutenção como ferramenta de acompanhamento
Os checklists são uma ferramenta auxiliar na manutenção, muito utilizados para controle e acompanhamento dos KPIs. Consistem em uma lista de pontos a serem verificados pelo técnico na realização de inspeções e visitas técnicas.
Com o checklist em mãos, a pessoa responsável pela inspeção possui um guia completo do que deve ser analisado para verificar se os ativos estão ou não em conformidade com os parâmetros e padrões exigidos.
Para medir os indicadores de manutenção escolhidos, a tecnologia é uma grande aliada. Assim, utilizar softwares e ferramentas digitais pode ajudar muito no acompanhamento de resultados, evitando erros manuais e proporcionando insights estratégicos.
Conheça os benefícios do Checklist Fácil
Falando em tecnologia para facilitar a gestão da manutenção industrial, você já conhece o Checklist Fácil? O software ajuda a padronizar processos, manter o sistema de manutenção industrial nos conformes e garantir que a operação esteja funcionando de forma eficaz.
O Checklist Fácil permite a coleta dos dados e análise de relatórios em tempo real, pois centraliza todos os dados colhidos durante as checagens e inspeções antes e após as manutenções. Isso permite um maior controle gerencial, bem como entendimento sobre a vida útil dos equipamentos.
Confira um exemplo de checklist de manutenção criado dentro do sistema:
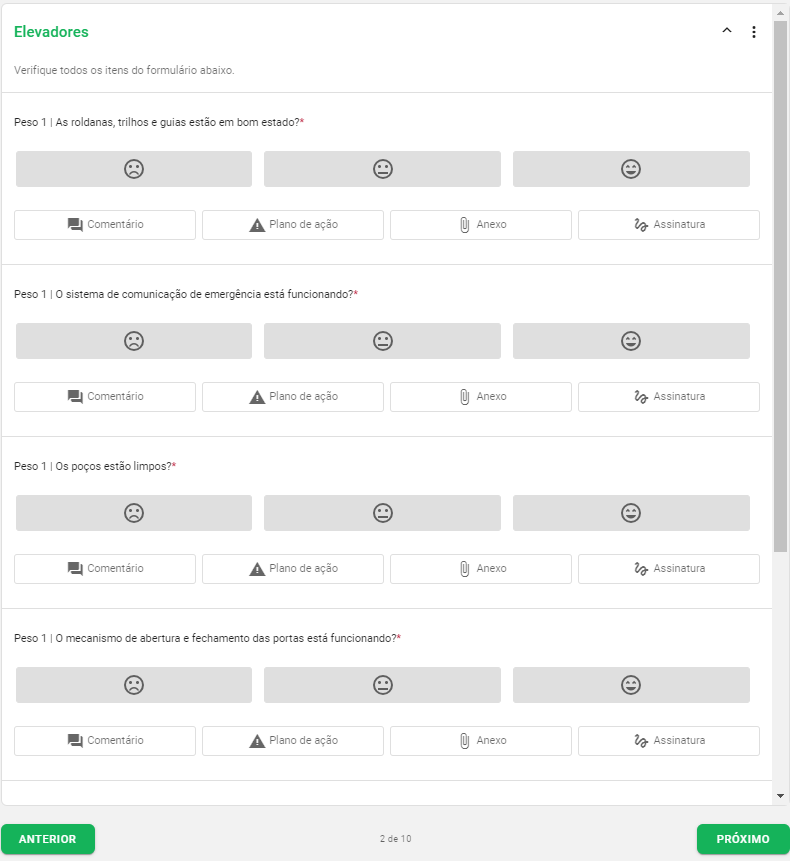
São mais de 150 recursos disponíveis, como:
- Checklists digitais personalizados;
- Planos de Ação automatizados;
- Workflows (fluxos de trabalho) inteligentes;
- Agendamento de checklists;
- Integração com Sensores IoT;
- Relatórios e dashboards completos;
- Integração com Power BI;
- Inclusão de mídias e preenchimento com imagens;
- Assinatura digital com validade jurídica.
Quer saber mais sobre como gerenciar seus processos de manutenção? Entre em contato e solicite uma demonstração gratuita.