A eficiência operacional da indústria pode ser mensurada de diversas maneiras, mas um dos indicadores mais essenciais para o setor com certeza é o OEE.
Você sabe calcular este indicador e qual a importância de monitorá-lo de perto? Confira neste artigo como fazer isso e as nossas dicas para melhorar a Eficiência Global dos Equipamentos.
Boa leitura!
Neste artigo você encontrará:
O que é OEE?
OEE é sigla em inglês para Overall Equipment Effectiveness ou Eficiência Global do Equipamento. Trata-se de um indicador de manutenção que mensura o desempenho de uma máquina ou equipamento, em relação à sua disponibilidade, produtividade e a qualidade de sua produção.
O OEE compõe a metodologia TPM ou Manutenção Produtiva Total, conceito de gestão criado por Seiichi Nakajima, que busca reduzir perdas, paradas e falhas nos processos produtivos, promovendo a melhoria contínua de todo o parque fabril.
Utilizado no contexto da indústria, o OEE é uma forma de medir o rendimento e a eficiência dos equipamentos, além do real valor agregado da produção, ou seja, quanto do tempo de operação do equipamento gerou faturamento para a empresa.
Para isso, é necessário considerar no cálculo outros três indicadores, como veremos a seguir.
Quais indicadores compõem o OEE?
Como falamos acima, o OEE considera três fatores: disponibilidade, produtividade e qualidade.
Disponibilidade
A disponibilidade indica o tempo em que o equipamento está produzindo efetivamente dentro do período total em que ele está disponível ou programado para produção.
Para calcular a porcentagem de disponibilidade do equipamento, basta dividir o tempo de operação real pelo tempo total em que ele está disponível para produção, multiplicando o resultado por 100%.
Consideramos como tempo total a soma do período em que a máquina está efetivamente produzindo e do período em que esteve parada para manutenções, ajustes, entre outros.
Por exemplo:
Um equipamento com disponibilidade total para produzir durante 23 horas em um dia ficou parado por 3 horas para manutenções não planejadas. Isso significa que o tempo real de produção foi de 20 horas. Sendo assim, o cálculo será o seguinte:
20h de produção real/ 23h de disponibilidade para produção X 100%
Taxa de disponibilidade = 89,95%
Em outras palavras, aquele equipamento produziu por aproximadamente 90% do tempo em que esteve disponível o dia.
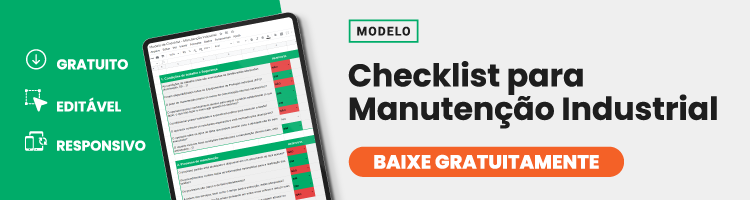
Produtividade
A produtividade do equipamento representa o quanto a máquina está produzindo em relação ao quanto ela deveria produzir, considerando como perda pequenas paradas que interrompam o processo produtivo.
A taxa de produtividade é obtida dividindo a produção real pela produção máxima esperada para aquele equipamento, e multiplicando o resultado por 100%.
Exemplo: supondo que uma máquina foi projetada com a capacidade de produção de 2 mil peças em um turno de 4 horas, mas produziu apenas 1,5 mil em determinado turno devido às paradas para ajustes. Neste caso, a taxa de produtividade caiu para 75%, como concluímos no seguinte cálculo:
1500 peças produzidas / 2000 peças em produção máxima X 100% = 75% de produtividade.
Isso significa que as paradas para realizar ajustes na máquina geraram uma perda de 25% da capacidade produtiva naquele turno.
Qualidade
A taxa de qualidade, por sua vez, diz respeito à quantidade de produtos que atendem todos os critérios dos padrões de qualidade dentre a produção total do equipamento.
Similar ao cálculo dos outros dois indicadores que compõe o OEE, a taxa de qualidade é o resultado da divisão do número de produtos bons pela quantidade total de produtos produzidos, os bons e os irregulares.
Então, digamos que uma máquina produziu 1,5 mil peças, mas apenas 1,3 mil estão dentro dos requisitos mínimos de qualidade. Assim, conclui-se que a taxa de qualidade daquela produção foi de 86%, ou seja:
1300 peças boas / 1500 peças produzidas X 100% = 86% de aproveitamento dos produtos com qualidade.
Quais são as seis perdas do OEE?
Como vimos, existem alguns fatores que impactam diretamente no índice de eficiência dos equipamentos. Paradas não planejadas para manutenção e ajustes, por exemplo, são alguns dos motivos pelos quais os equipamentos podem apresentar um OEE longe do ideal.
Chamamos isso de perdas, ou as seis grandes perdas do OEE, que são categorias de ineficiências que podem afetar a produtividade e o desempenho de um equipamento ou processo de produção. São elas:
- Setup ou perda por paradas planejadas: é o tempo em que a máquina permanece inativa para trocas de ferramentas, ajustes de configuração ou preparação para a produção de um novo produto. É o tempo que não está sendo utilizado para a produção efetiva.
- Falhas ou perda por paradas não planejadas: é o período em que a máquina fica inoperante devido a falhas mecânicas, elétricas ou outros problemas não previstos.
- Redução de velocidade ou perda por queda de velocidade: tempo em que a máquina opera abaixo da sua capacidade máxima por limitações ou restrições no processo.
- Defeitos ou perda de qualidade: Refere-se ao tempo perdido devido à produção de produtos defeituosos que precisam de retrabalho ou rejeição. Isso inclui o tempo para identificar, corrigir ou descartar os produtos com defeito.
- Perda por pequenas paradas e ajustes menores: Inclui pequenas interrupções na produção que podem parecer insignificantes, mas que, ao longo do tempo, somam uma quantia significativa de tempo perdido.
- Subtilização ou perda por produção abaixo da capacidade máxima: Representa o tempo em que a máquina está operando, mas não está produzindo na sua capacidade máxima.
Como calcular o OEE?
Para calcular o OEE é bastante simples: com os indicadores de disponibilidade, produtividade e qualidade mensurados, basta multiplicar as porcentagens de cada um deles. Assim:
OEE = disponibilidade (%) x produtividade (%) x qualidade (%)
O ideal é que a indústria opere com 100% de eficiência ou próximo disso. Vamos retomar os cálculos que vimos anteriormente para descobrir a Eficiência Global do Equipamento em mais um exemplo:
Disponibilidade: 90%
Produtividade: 75%
Qualidade: 86%
Logo, vamos obter o OEE a partir da seguinte operação:
OEE = 90% x 75% x 86%
A Eficiência Global do Equipamento do nosso exemplo é de aproximadamente 58%.
Por que é importante calcular o OEE?
O OEE é um KPI muito importante, principalmente para melhoria contínua dos processos que envolvem a produção realizada por esses equipamentos.
O cálculo do OEE é essencial para identificar, quantificar e prevenir as perdas que ocorrem ao longo do processo produtivo. Afinal, cada uma dessas perdas representa uma área de oportunidade para a melhoria dos processos e operações de produção.
O OEE e o mapeamento das perdas ajudam a identificar onde estão ocorrendo as ineficiências e as áreas que precisam de melhoria. Isso permite priorizar ações com base em seu impacto sobre o OEE e direcionar esforços e recursos para as áreas mais críticas.
O cálculo e o monitoramento desse indicador permitem ainda:
- Reduzir custos com o tempo ocioso das máquinas;
- Minimizar retrabalhos de produtos defeituosos;
- Aumentar a eficiência e a produtividade;
- Melhorar a qualidade dos produtos;
- Promover uma cultura de melhoria contínua;
- Aumentar a competitividade;
- Reduzir custos operacionais como um todo;
- Tomar decisões precisas e bem embasadas sobre o indicador OEE.
Como melhorar o OEE?
Como vimos, melhorar aspectos relacionados à disponibilidade, produtividade e qualidade no desempenho dos equipamentos impacta diretamente no OEE e, consequentemente, na eficiência de toda a indústria. Mas, por onde começar a melhorar o indicador OEE? Confira algumas estratégias:
Implemente manutenções preventivas e preditivas
Estabeleça um programa de manutenção preventiva para realizar inspeções e reparos regulares e utilize técnicas de manutenção preditiva para monitorar as condições dos equipamentos e identificar sinais de desgaste ou falhas iminentes.
Uma forma de otimizar as manutenções é planejá-las e agendá-las, de forma que não atrapalhe a disponibilidade e a eficiência dos equipamentos.
Capacite a equipe que opera os equipamentos
Um treinamento adequado aos operadores do parque fabril garante o uso correto de máquinas e equipamentos, além de agilizar a identificações de problemas ainda em seu início e otimizar pequenas manutenções, diminuindo a ociosidade por setup ou falhas.
Reduza o tempo de Setup
Falando em Setup, minimizar o tempo de configurações e trocas para produção de diferentes produtos é uma estratégia que ajuda a aumentar o tempo de disponibilidade das máquinas. Consequentemente, o equipamento produzirá cada vez mais próximo de sua capacidade total em menor tempo.
Monitore e avalie os equipamentos regularmente
Estabeleça uma rotina de checagem e avaliação da eficiência dos equipamentos para antecipar necessidades de modificações, atualizações e substituições para aumento de desempenho e confiabilidade.
Uma dica é utilizar sistemas que facilitem o monitoramento em tempo real para detectar e responder rapidamente a problemas ou falhas antes que causem grandes interrupções na produção.
A melhor forma de fazer isso é contar com o Checklist Fácil para otimizar processos de checagem como auditorias e inspeções, e acompanhar dados em tempo real a partir da coleta de informações via formulários digitais.
Aumente a eficiência operacional da sua indústria com o software de checklists digitais líder na América Latina e o mais completo do mercado.
Peça uma demonstração e conheça as mais de 150 funcionalidades do Checklist Fácil!