A manutenção detectiva identifica falhas em sistemas e equipamentos antes que elas aconteçam ou se tornem críticas. Por meio de monitoramento e inspeções regulares, utilizando sensores e análises preditivas, consegue prever eventuais falhas, trazendo confiabilidade, redução de custos e minimização do tempo de inatividade do maquinário.
_______________________________________________
A complexidade dos equipamentos, sensores, circuitos e chips fez com que a manutenção detectiva se tornasse essencial para analisar a sustentabilidade desses sistemas automatizados.
Com a quarta revolução industrial, a tecnologia e a digitalização se tornaram onipresentes no dia a dia, levando a automação para todos os cantos – do chão de fábrica ao escritório. Talvez, em breve, até ao setor de transporte e logística.
Essas máquinas precisam funcionar perfeitamente, e muitas falhas podem ser imperceptíveis até causarem problemas maiores. Assim, detectá-las antecipadamente é crucial para os resultados da indústria. Entenda melhor sobre esse assunto, seguindo a leitura do nosso conteúdo.
Neste artigo você encontrará:
O que é manutenção detectiva?
Manutenção detectiva é o tipo de inspeção que visa se adiantar a eventuais falhas que possam afetar máquinas e equipamentos.
É uma espécie de investigação, cujos procedimentos inspecionam e testam os componentes desses instrumentos operacionais, com o objetivo de levantar problemas que estejam em fase inicial e ainda não apresentem consequências aparentes.
Essa também é uma forma de encontrar falhas mascaradas, ou seja, escondidas no emaranhado de componentes eletrônicos.
Visto que o universo industrial está adotando equipamentos cada vez mais autômatos, a manutenção detectiva torna-se essencial para que sejam revelados defeitos imperceptíveis. Que, sem o devido conserto, poderiam causar perdas devido ao seu agravamento ao longo do uso.
Por meio de recursos tecnológicos de última geração, os sistemas de inteligência fazem os testes e analisam o desempenho do equipamento.
A partir dos dados coletados, informam o status de cada componente. Isto é: se ele está funcionando da sua melhor forma, se o uso está adequado, se há algo de errado no composto de peças ou se há potencial de risco para um dano maior.
Por essa característica, a manutenção detectiva é considerada um tipo de manutenção proativa, que visa antever eventuais falhas em um equipamento.
Com o advento da indústria 4.0 e a digitalização dos processos, as empresas vêm implementando esse tipo de manutenção em maior escala. Isso porque as máquinas estão mais sensíveis, devido aos inúmeros itens eletrônicos, sensores e chips. Logo, precisam ser constantemente vistoriados para garantir sua qualidade e sustentabilidade.
Sendo assim, adotam o chamado Teste de Detecção de Falhas (TDF), visando encontrar erros incipientes nos seus instrumentos de trabalho e de chão de fábrica. Para, com isso, agir antes que se tornem maiores, causem prejuízos ou tragam riscos à segurança do trabalho ou ao meio ambiente.
Qual a importância da manutenção detectiva industrial?
A manutenção detectiva industrial é extremamente importante para as fábricas, já que pode evitar “dores de cabeça” com problemas maiores, como falhas que causam paradas na produção ou acidentes.
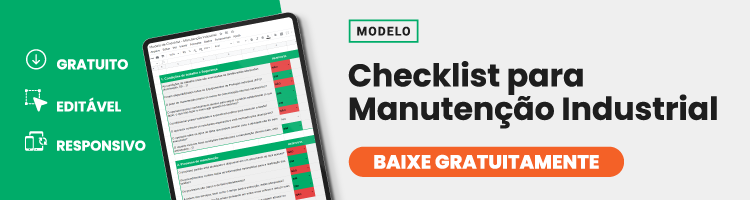
Com ações que detectam eventuais erros que podem acontecer, a empresa ou o profissional envolvido consegue agir preventivamente, acionando uma manutenção corretiva planejada.
Com isso, garante a segurança da operação como um todo, evitando prejuízos e atrasos, e minimizando diversos tipos de riscos.
Outra grande vantagem da manutenção detectiva é a ampliação da vida útil de um equipamento, já que, por suas complexidades, representam um investimento considerável.
Um exemplo de utilidade da manutenção detectiva na indústria automobilística acontece junto com a execução das manutenções preventivas programadas dos veículos nas concessionárias.
Quando um veículo sai da loja, zero quilômetro, o proprietário leva consigo o manual com as datas em que deverá levar o automóvel na concessionária para fazer uma manutenção programada.
Ao encostar o carro na oficina, seus componentes mecânicos e eletrônicos passarão por uma série de testes, que irão avaliar o desgaste das peças e sensores, a fim de investigar se há algo errado no sistema.
Muitas vezes, com os dados coletados nestes testes detectivos, são relatados resultados de desgaste de elementos por mau uso do motorista, por exemplo. Assim como podem ser levantados problemas de fabricação.
Dessa forma, é possível corrigir essas falhas iminentes e evitar panes e acidentes.
Já em uma indústria, a detecção de uma eventual falha ainda em processo inicial poderá evitar danos à empresa e, até mesmo, ao meio ambiente. Como no caso de acidentes de maiores proporções que causem impactos ambientais, como o vazamento de resíduos tóxicos em um rio, por exemplo.
Quais falhas podem ser detectadas neste tipo de manutenção?
Por meio dos Testes de Detecção de Falhas, podem ser verificados na manutenção detectiva:
- Desgastes de peças e sensores internos;
- Deterioração por mal uso, uso excessivo ou em ambiente inadequado;
- Corrosão de componentes mecânicos ou eletrônicos;
- Corrosão de metais;
- Esfacelamento de fios elétricos que podem causar curto circuitos;
- Estresse de itens mecânicos;
- Envelhecimento de materiais e do equipamento em si, entre outros.
Essas falhas podem ser divididas em 13 diferentes categorias, de acordo com sua proporção e forma como acontecem. Confira em detalhes:
1. Falhas catastróficas ou estruturais
Geralmente de grandes proporções, este tipo de falha verificada na manutenção detectiva é aquela que pode causar prejuízos imensuráveis para a indústria. Se não corrigida a tempo, pode gerar acidentes graves com o operador e até mesmo a perda do equipamento.
Algumas falhas como essa acontecem quando fios elétricos estão se encostando, podendo provocar curtos circuitos, ou quando a tubulação de ar comprimido apresenta rachaduras que podem se tornar vazamentos maiores, originando até incêndios.
2. Falhas simples
São consideradas falhas simples aquelas que afetam apenas um item da composição do equipamento – e este não representa um risco maior.
3. Falhas permanentes
Estas falhas são aquelas que, como já diz o nome, são irreparáveis. Neste caso, cabe ao gestor de manutenção solicitar a troca da peça inteira, se possível.
Se não for viável, deverá comunicar ao Gestor de Produção Industrial o status do equipamento: se há possibilidade de continuar usando sem riscos ou se a máquina deverá ser descartada.
4. Falhas intermitentes
As falhas intermitentes são as que acontecem periodicamente. Elas devem ser corrigidas para que não atrapalhem a produção, causando atrasos nas entregas da indústria.
5. Falhas de parâmetros ou paramétricas
Detectadas por sistemas computadorizados, as falhas de parâmetros ou paramétricas são verificadas quando há diferença de valores nas medidas ideais apontadas pelo fabricante do equipamento.
Por exemplo, o parâmetro correto de determinada máquina é atuar entre >15 e <45, e na medição da manutenção detectiva apresentou um valor abaixo ou acima do aceitável para a normalidade.
Esse tipo de falha é muito comum quando se fazem análises de fadiga dos equipamentos automatizados.
6. Falhas independentes
Essas são consideradas as falhas em que o profissional de manutenção não encontra uma interligação entre a causa e seus efeitos.
Ou seja, em um processo de inspeção detectiva, localiza-se determinada falha em um componente. Mas, essa falha não é causadora de um ruído inespecífico que o equipamento vem fazendo.
7. Falhas múltiplas
São elencadas como falhas múltiplas os erros encontrados em diversos itens que compõem o equipamento, ao mesmo tempo. Elas podem ter acontecido simultaneamente ou serem dependentes umas das outras, como vemos a seguir.
8. Falhas dependentes
Praticamente uma subcategorização das falhas múltiplas, as falhas dependentes ocorrem quando é detectada uma causadora das demais falhas verificadas.
9. Falhas dominantes
Também pode ser considerada uma subcategorização das falhas múltiplas, já que essa predomina frente a outros defeitos que acontecem ao mesmo tempo.
10. Falhas isoladas ou detectáveis
São as falhas conceituadas como de fácil localização. Em uma verificação detectiva, logo o sistema localiza essa falha única, que é rapidamente reparada.
11. Falhas equivalentes e indistintas
Também dentro da categoria de falhas múltiplas, as equivalentes são localizadas em um mesmo equipamento e suas implicações são as mesmas. De forma que se torna impossível definir qual prevalece ou causa maior preocupação.
12. Falhas mascaráveis
Essas falhas são bastante preocupantes, já que não são facilmente localizadas. Elas podem ficar, como já diz o nome, mascaradas em algum item ou local, impedindo sua detecção.
Aparentemente, o sistema está livre de defeitos, causando uma percepção equivocada de normalidade por um determinado período.
13. Falhas não observáveis ou indetectáveis
Em sistemas automatizados, essas falhas são a “dor de cabeça” do gestor de manutenção.
Diferente das mascaráveis, essas falhas não fazem parte do sistema de detecção de falhas dos fabricantes, e só podem ser resolvidas com manutenções corretivas.
Qual a diferença entre manutenção detectiva, preventiva, preditiva e corretiva?
Primeiramente, é necessário compreender que as manutenções são essenciais no dia a dia. Isso porque as máquinas facilitam nossa vida, rotina e a produtividade das indústrias. Sem falar que elas estão suscetíveis a desgaste com o tempo e o uso constante.
Segundo a Associação Francesa de Normalização (AFNOR), na sua NF 60-010, “manutenção é o conjunto de ações que permitem restabelecer um bem para o seu estado específico ou medidas para garantir um serviço determinado”.
Já para Paulo Samuel de Almeida, no livro Gestão da Manutenção aplicada às áreas industrial, predial e elétrica, manutenção “pode ser definida como um conjunto de cuidados e procedimentos técnicos necessários ao bom funcionamento e ao reparo de máquinas, equipamentos, peças, veículos, instalações prediais, elétricas, moldes e estampos”.
Sendo assim, com o advento da revolução industrial, as máquinas tomaram conta dos setores produtivos das fábricas, obrigando-as a adotarem processos de manutenção constantes, surgindo os conceitos de manutenção preventiva e corretiva.
Atualmente, com a 4º Revolução Industrial, a onipresença da tecnologia no ambiente produtivo fez com que os gestores verificassem a necessidade de mais dois tipos de manutenções: a preditiva e a detectiva.
Para entender melhor essas diferenças nos tipos de manutenções, siga essa leitura.
Manutenção preventiva
A manutenção preventiva tem como objetivo prevenir eventuais falhas que podem acontecer com o uso contínuo de uma máquina ou equipamento. Se compararmos com o corpo humano, seria aquela visita ao médico com regularidade para exames de checkup.
Na manutenção preventiva, a equipe deverá realizar um plano de ação para a sua realização.
Neste plano, será feito o agendamento da data para o diagnóstico do equipamento e análise da vida útil das peças, levando em consideração seu estado atual, históricos e relatórios anteriores.
Caso haja necessidade, serão feitos ajustes e lubrificações para que a máquina siga em seu perfeito funcionamento.
Manutenção corretiva
A manutenção corretiva é vista como necessária no momento em que o equipamento já manifesta problema. Comparando também com o corpo humano, essa é a hora em que alguma dor ou fratura nos faz procurar um médico.
Um barulho diferente do comum no cotidiano, uma luz de alerta, fumaça, cheiros estranhos ou uma parada repentina são sintomas de que há uma falha que precisa ser consertada.
Nesta situação, o gestor de manutenção deverá verificar se há como fazer uma manutenção corretiva não planejada, ou seja, parar tudo e consertar. Ou se há possibilidade de continuar trabalhando com a máquina até um momento mais oportuno para o conserto.
Para chegar a essa conclusão, ele deverá analisar vários fatores como: riscos de parar por completo, de danificar outras máquinas, à saúde e a vida do operador, à empresa e, até mesmo, riscos de ocasionar impactos ambientais.
Manutenção preditiva
A manutenção preditiva é aquela que se antecipa a correção de problemas.
Segundo Paulo Samuel de Almeida, ainda no livro Gestão da Manutenção aplicada as áreas industrial, predial e elétrica, a manutenção preditiva é conhecida entre os mecânicos das indústrias como “ouvir a máquina”.
Por meio de instrumentos específicos para medições, os técnicos verificam temperatura, vibrações, ruídos excessivos, gasto de lubrificantes, entre outros, e seguem acompanhando esses fenômenos por um tempo, para definir se há necessidade de acionar uma manutenção corretiva programada.
Manutenção detectiva
Devido às novas formas de possuir e usar equipamentos, as empresas precisam, cada vez mais, fazer uso desse tipo de manutenção, que visa detectar falhas antes mesmo que elas aconteçam.
Pense na situação: uma pessoa aluga um carro para uma viagem. Após alguns dias, o devolve à locadora. Antes desse veículo ser entregue a outro locador, ele precisa passar por uma manutenção detectiva.
O objetivo aqui é verificar se todos os itens, peças, circuitos e componentes estão em perfeito estado, para que o carro possa ser alugado por outra pessoa.
É responsabilidade da empresa locadora do veículo fazer essa revisão, a fim de garantir a segurança dos clientes.
Muitas indústrias também alugam equipamentos, e esses devem passar pelo mesmo processo.
Outro exemplo da necessidade de manutenção detectiva acontece no agronegócio.
Hoje em dia, granjas de frangos com milhares de aves são controladas por equipamentos computadorizados, que precisam passar por manutenções detectivas constantemente.
Isso porque uma falha nesses sensores poderá custar a vida desses animais e um prejuízo imenso para o negócio.
Por que uma gestão eficiente é importante para manutenção detectiva ser um sucesso?
Fazer uma gestão eficiente é de extrema importância para o sucesso da manutenção detectiva. Ela inclui planejar minuciosamente os processos e gerenciar recursos como técnicos e tecnologias. Através disso, é possível:
- Determinar quais equipamentos serão inspecionados;
- Avaliar a periodicidade (criando uma rotina de testes);
- Analisar e considerar as orientações dos fabricantes dos equipamentos;
- Desenvolver estratégias de conserto e reparação;
- Criar relatórios e gerar históricos das manutenções.
Com tudo isso, chega-se a conclusão das 5 vantagens da gestão eficiente da manutenção detectiva:
- Previsão de custos no planejamento anual do setor;
- Levantamento fácil de verbas para correções necessárias;
- Evitar paradas não programadas e atrasos na produção;
- Antecipar a contratação de mão de obra e a compra de insumos para reparos;
- Maior assertividade em todo o processo garante melhores resultados para o todo.
Implementar técnicas e metodologias para gestão eficiente de manutenções detectivas faz parte de um processo maior de melhoria contínua, que muitas indústrias estão implementando em seus processos produtivos.
Quando aplicar a manutenção detectiva?
Como você já viu, a manutenção detectiva é benéfica dentro da indústria, se adiantando em relação a possíveis falhas e problemas. Entretanto, existem algumas situações e contextos nos quais ela é extremamente indicada. Veja alguns exemplos:
- Equipamentos críticos, nos quais alguma falha pode resultar na paralisação da produção, danos ambientais ou riscos à segurança dos trabalhadores, por exemplo;
- Equipamentos com histórico de falhas, que apresentam problemas recorrentes e imprevisíveis;
- Equipamentos com custo elevado, afinal, a manutenção desse tipo de maquinário exige um alto investimento (e, muitas vezes, fora do orçamento planejado);
- Equipamentos complexos, em que muitas variáveis podem influenciar seu desempenho e integridade, como máquinas rotativas, sistemas de refrigeração e equipamentos de alta pressão;
- Equipamentos de operação contínua, como aqueles que funcionam 24h por dia e uma paralisação não planejada por ter sérios impactos;
- Equipamentos cuja operação está relacionada à normas regulatórias, comuns em indústrias como a farmacêutica e alimentícia.
Quais são as fases da manutenção detectiva?
Para garantir que os problemas sejam identificados e corrigidos antes que causem falhas, é preciso criar um processo muito bem estruturado. Algumas fases indispensáveis devem fazer parte de processo, como:
Gestão de máquinas e equipamentos
O primeiro passo é realizar um inventário, mapeando e registrando as informações de todos os equipamentos da empresa. Então, será possível definir quais devem entrar no plano de manutenção detectiva e com qual prioridade, observando itens críticos. Nesse contexto, a aplicação de checklists é muito útil para garantir o mapeamento e a priorização corretas. Confira abaixo o trecho de um Modelo de Checklist para Avaliação de Tratores e Máquinas, que pode ser baixado na íntegra sem nenhum custo!
Garantia de capacidade técnica
Com o mapeamento das máquinas em mãos, muitas empresas partem direto para a ação. Entretanto, existe um fase anterior que não pode ser deixada de lado: é preciso garantir que os recursos necessários para realização as manutenções estejam em conformidade.
Aqui, considere mão de obra, tempo, materiais, disponibilidade da equipe técnica e capacitação do time. Se necessário, invista em treinamentos para profissionalizar ainda mais os envolvidos.
Cronograma
A implementação da manutenção detectiva precisa contar com previsibilidade. Por isso, crie um cronograma de manutenção para acompanhar o desempenho das máquinas e aplicar as ações necessárias.
Fluxos de trabalho
Para que a manutenção ocorra de forma correta e eficiente, é preciso definir qual será o fluxo de trabalho, estabelecendo prazos, pessoas e times responsáveis, planos de ação, etc.
Para ajudar nesse processo, o Checklist Fácil conta com o recurso de Workflow, para que você vincule checklists a diferentes etapas de execução, padronize fluxos de trabalho para cadenciar as etapas da operação e garanta a ordem correta das execuções.
Como fazer uma boa gestão da manutenção detectiva industrial
A gestão de manutenção detectiva industrial tem uma importância gigante na otimização dos processos e na redução real de custos.
Isso tudo devido a estar intimamente relacionada com o bom funcionamento das máquinas e equipamentos que fazem a indústria produzir sempre mais e melhor.
Assim, para garantir a total funcionalidade da fábrica, com “equipamentos a todo o vapor”, implementar uma estratégia de PCM – Planejamento e Controle de Manutenção será o divisor de águas na história de uma organização.
Como já diz o nome, essa metodologia de gestão de trabalho é divida em 3 principais passos.
Confira a seguir:
1. Planejamento de manutenção – o plano de ação
Nesta etapa do PCM, o gestor de manutenção deverá:
- Determinar quais máquinas devem ser inspecionadas na manutenção detectiva;
- Estabelecer quem serão os responsáveis por tal manutenção, contando sempre com equipe especializada e experiente;
- Delimitar quais sistemas e equipamentos serão utilizados no processo de detecção de falhas;
- Decidir sobre a rotina de checagem, determinando dia, horário, periodicidade, tempo estimado, insumos e profissionais envolvidos;
- Definir quais equipamentos podem ter ser testados ligados, em operação, ou devem ser parados (desligados), para que não haja prejuízos;
- Esclarecer quais as soluções para as falhas encontradas;
- Escolher metas e indicadores;
- Registrar todas as informações importantes sobre a manutenção numa ferramenta ou arquivo facilmente acessível pela equipe.
Visto estas especificações, uma solução de tecnologia como o checklist online pode ser muito eficiente.
Com uma ferramenta como essa, é possível criar um checklist de TDFs, registrando em detalhes as atividades de cada manutenção e o status de cada componente ou peça, para fácil e rápido acesso.
BAIXE GRÁTIS | Kit Estratégico para Plano de Ação
2. Controle de manutenção
A parte de controle de manutenção também exige inteligência e bom relacionamento do gestor de manutenção.
Ele deverá estar a par de tudo o que está sendo realizado, se está sendo feito da forma correta e analisar se estão adequadas ao planejamento desenvolvido, para verificar se não há inconformidades no processo.
Nesta etapa, o gestor também precisa analisar os indicadores definidos no planejamento, fazendo comparações importantes e analisando padrões, para a tomada de decisões seguras e eficientes.
3. Execução da manutenção
Chegou, enfim, a hora da “mão na massa”. ou seja, o momento de fazer a manutenção detectiva.
Neste momento, o gestor deverá acompanhar de perto a manutenção, conferindo a “ligação” dos sensores e o levantamento de dados.
A manutenção detectiva vai verificar o estado de conservação do equipamento e de seus componentes e, caso haja alguma falha seja detectada, o gestor deverá tomar a frente na definição por uma ação de correção imediata – seja uma parada ou mesmo o descarte do equipamento.
Esse tipo de manutenção visa assegurar a maior vida útil das máquinas, para que a organização como um todo alcance seus melhores resultados.
Visto dessa forma, percebe-se que o PCM não tem início, nem fim. Sendo um ciclo em que uma etapa apoia a outra, otimizando processos e recursos e fortalecendo a indústria, para que possa buscar o seu fim: o melhor resultado operacional.
De que forma a tecnologia é decisiva na gestão da manutenção detectiva industrial?
A tecnologia é fundamental na manutenção detectiva industrial, visto que os equipamentos elétricos e eletrônicos estão tomando conta de diferentes funções e atividades antes executadas pelo homem.
O objetivo dessa tecnologia não é substituir o ser humano, mas sim agregar conhecimento, dados e informações que podem ser decisivas na hora de uma tomada de decisão.
Quais são os sistemas de proteção para manutenção detectiva?
Softwares e sistemas computadorizados fazem testes periodicamente nos equipamentos para que qualquer parâmetro alterado seja verificado a tempo de um conserto, sem problemas de maiores proporções.
Algumas dessas tecnologias decisivas são:
- Painéis de controle com sinalização de alarmes, alertas e notificações;
- Computadores supervisórios;
- Computador Lógico Programável (CPL);
- Sensores IoT;
- Sistemas para testes em dispositivos de segurança como detectores de incêndio, sensores de vazamento de ar comprimido, de lubrificantes etc.
Como usar checklists na manutenção detectiva?
Outra solução de tecnologia importantíssima para as checagens detectivas são as ferramentas de checklist online. Os checklists são grandes aliados para o controle de qualquer tipo de manutenção e podem ser usados em diversas aplicações, como:
- Criação de listas de verificação personalizadas;
- Listagem de tarefas de inspeção e monitoramento:
- Identificação de pontos críticos;
- Especificação de critérios de aceitação para parâmetros como temperatura, vibração, pressão etc;
- Documentação e descrição de não conformidades;
- Criação de planos de ação;
- Agendamento de inspeções e atualizações.
Qual o melhor software para aplicar a manutenção detectiva?
Com mais de 1.500 clientes em 14 países, o Checklist Fácil é a ferramenta mais completa para padronização e digitalização de checagens e processos, proporcionando eficiência, qualidade e controle nas manutenções. Líder de mercado na América Latina, o software oferece mais de 150 funcionalidades para potencializar sua operação.
Com o Checklist Fácil, é possível agendar checklists para inspeções periódicas, inserir respostas com fotos e vídeos, configurar Workflows e automatizar a criação de planos de ação sempre que uma não conformidade for detectada durante a checagem, garantindo a aplicação das ações corretivas.
Confira, na imagem abaixo, um exemplo de checklist para PMOC (Plano de Manutenção, Operação e Controle) dentro do nosso sistema:
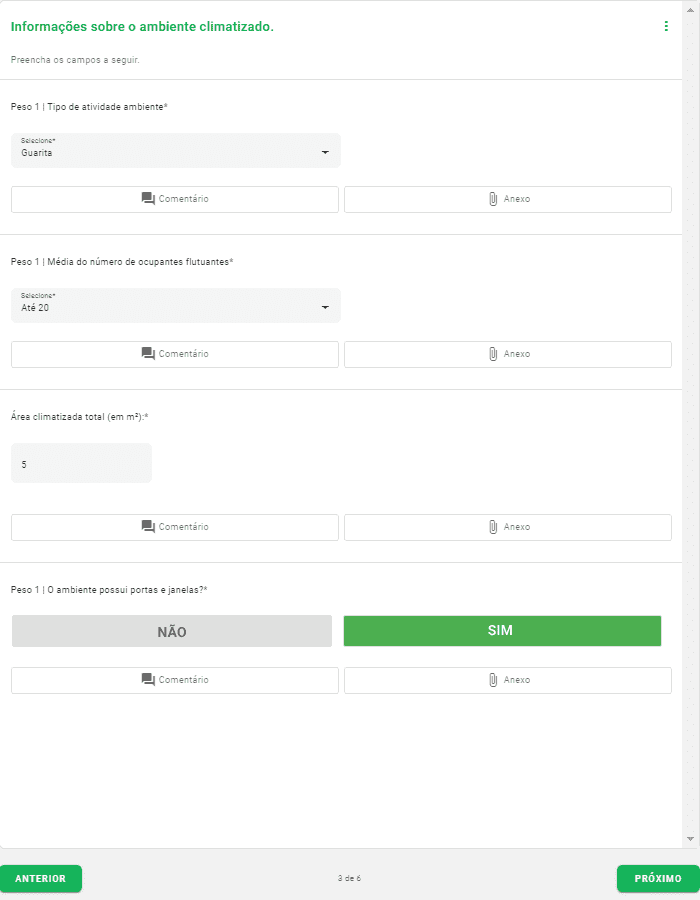
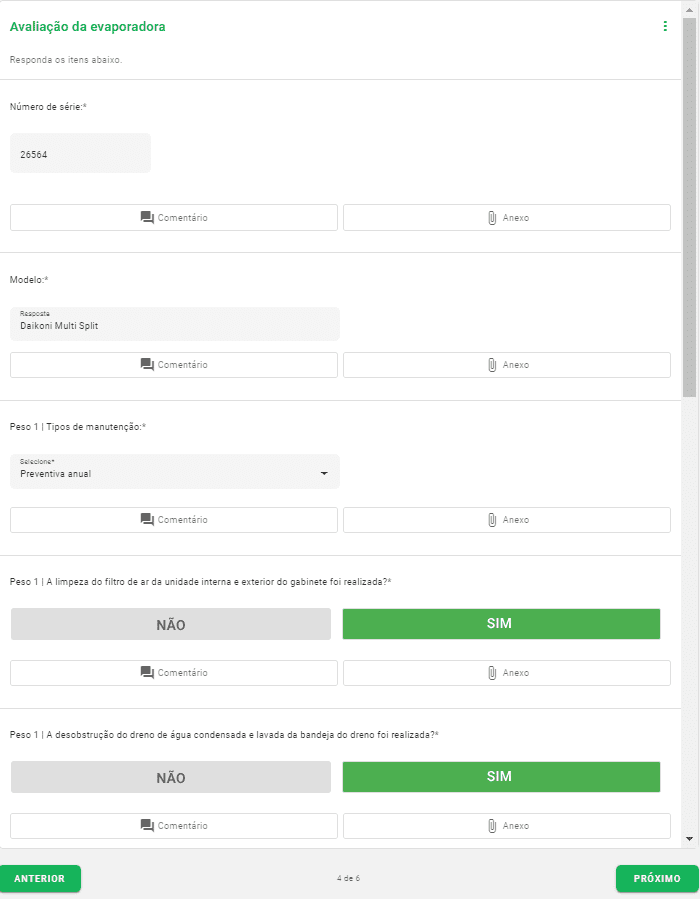
Todos os dados coletados durante as aplicações dos checklists são utilizados para popular dashboards completos e personalizados, facilitando a visualização de informações e relatórios para acompanhar a eficiência das suas manutenções e identificar gargalos.
Além disso, o Checklist Fácil pode ser integrado diretamente a dispositivos IoT para realizar medições de temperatura, umidade, pulsos elétricos e outros comportamentos em tempo real, garantindo as condições de funcionamento corretas do seu maquinário. Se algum parâmetro estiver fora da normalidade, o software pode enviar uma notificação e acionar um plano de ação ou a aplicação de um checklist para realizar as verificações necessárias. Tudo de forma automatizada!
Para ver como nossa solução funciona na prática, que tal agendar uma demonstração gratuita com um especialista, ou fazer um teste grátis? Conheça agora o software que vai revolucionar não apenas sua operação de manutenções, mas todos os processos da sua empresa!